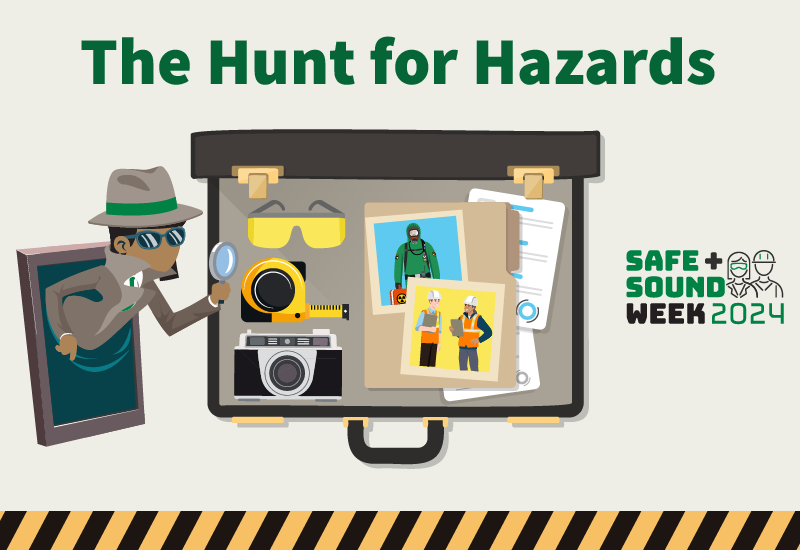
All workplaces have job hazards. Whether you are a construction worker working at heights, an agricultural worker handling a chemical substance, or a warehouse worker lifting heavy objects, these hazards can cause injurie, illnesses, and even deaths.
What is a job hazard analysis?
A job hazard analysis, or JHA, helps you identify and control unrecognized hazards, as well as hazards that might emerge when there are changes such as a new process or piece of equipment.
The goal of any JHA is to discover:
Potential consequences and worst-case scenarios
How an incident could happen
Contributing factors
The likelihood that an incident could occur
Hazard controls
This ongoing process of identifying and assessing hazards and hazardous situations is a critical part of any effective safety and health program.
Job hazard analysis steps
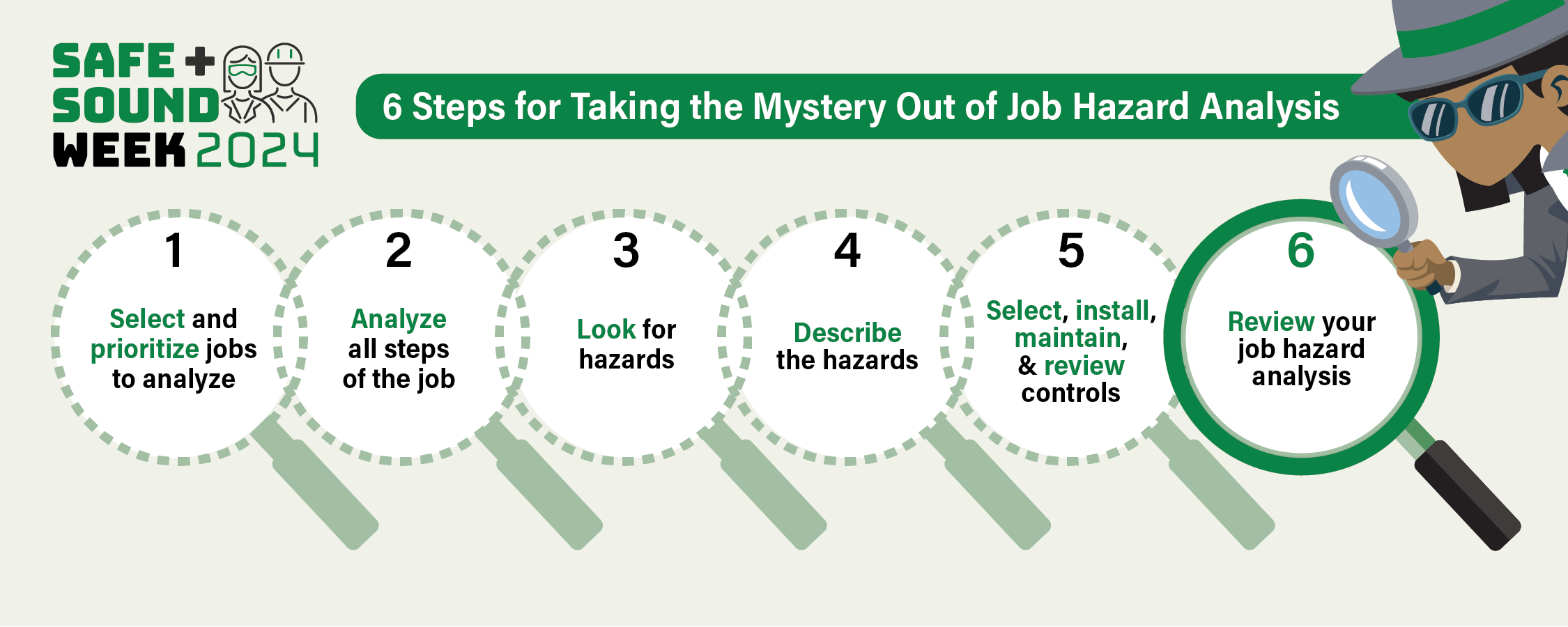
1. Select and prioritize jobs to analyze
When conducting a JHA, start with the jobs where a potential injury or illness could be severe or the jobs that frequently result in injuries or near misses when performed. Engage ALL your workers and review your records to help you decide.
2. Analyze all steps of the job
After you select the job to analyze, detail all aspects of the job performed. This is critical so that workers can review the JHA and best prepare to safely complete the job. You can make videos and take photos to help record this process.
3. Look at each step of the job for hazards
Next, identify all the hazards associated with the job. Review all previous injury or illness records and consider the worst-case scenarios that the hazards could cause. Hazards can typically be broken down into these categories: machine-related, physical barriers, biological, chemical or ergonomic.
4. Describe the hazards
Now that you have identified the job hazard, put on your detective hat to determine: Who does the hazard affect? What causes the hazard? What are other contributing factors? When is the hazard likely to impact workers? Where does the operation occur? Lastly, why would an accident occur?
5. Select, install, maintain and review controls
After you describe the hazards, explain the most effective way to control the hazard and prevent injuries. Refer to the hierarchy of control methods that includes 1) elimination, 2) substitution, 3) engineering controls, 4) administrative controls and 5) personal protective equipment.
6. Review your job hazard analysis
Congratulations! You developed a JHA! As a last step, be sure to review the JHA and continually update it as aspects of the job change or evolve.
Sign up for Safe + Sound Week!
Ready to put a JHA into action? This August, join us for Safe + Sound Week as we complete The Hunt for Hazards to uncover hazards while completing a job hazard analysis. Sign up to participate in Safe + Sound Week and join the conversation online using #SafeAndSoundAtWork.